The past few days were spent constructing the bases for my center work bench/table and lathe base. The center work bench top is 54" x 64" x 2-1/4" maple and weighs a ton. Good thing I put it on casters so I can move it around. It is interestingly reminiscent of Darryl and Cathy's kitchen center island. I also mounted two wood vises.
Next tasks will be to make a base to hold the table saw along with a router table. Both will end up being flush with the new work top so I can saw larger sheets of plywood, using the work top as the outfeed.
The lathe base is made from 6x6 fir posts. I may need to add some sand ballast to weigh it down which helps when doing the initial rough cut of out-of-round chunks of wood.
The Cabin
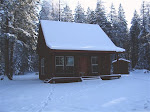
Monday, December 19, 2011
Tuesday, December 13, 2011
Log Cabin Wood Shop - Inside and Move-in
Since my last post we have completed the interior of the shop. This included the ceiling and gable 1x6 tongue and groove, the trim around the walls and windows, the lights, and the electrical. So, the inside is done. We were able to move all of the equipment from the garage into the shop...what a cool thing.
The garage is now wide open ... almost room to park another car!
In the shop, I have been organizing and putting things away, but there is still quite a bit of work to do. Many thing aren't where they will end up... but at least it's clean. I plan on building a large workbench in the middle of the room, using a 40" x 8' maple top I acquired with the help of my brother Darryl. I will also construct a lathe bench, a grinder table, build a miter bench area, and build shelves to store completed projects.
The large work table will sit where the table saw is show above.
It is so cool to have a large heated space to work on fun projects!
Sunday, November 27, 2011
Log Cabin Wood Shop - Roof Completed ... Really!
Saturday, November 19, 2011
Log Cabin Wood Shop - Snow, Door and Stove
The good news is that we received the metal roofing for the shop ... the bad news is that we now have 9" of snow on the ground which is likely to stick around until March. So, putting up roofing is not likely to happen.
We installed the wood stove and fired it up. This is a old Washington Stove Works "trash burner" that we bought around 10 years ago, originally
intended to be put in the big cabin. It is kitchen cabinet size, so I suspect it originally went in a kitchen along side cabinets. The upper part is the fire box which is really small, so it only handled kindling size wood or small logs around 3" diameter and 15' long. It has a a cook top, a built in damper and a removable soot box.
The past two days were spend building and installing the front door. It is made from 2x6 tongue and groove pine (same as the floor). As mentioned before, it is made as a dutch door, but I haven't cut it half yet. I still need to put in weather stripping and a door knob. Deb was disappointed that the cool cross supports are on the inside, rather than outside, so I may add more stuff on the outside. I bought some 15" gate hinges on ebay, which work really well.
Tomorrow, I'll probably frame in the windows and maybe start in on finishing electrical.
Wednesday, November 16, 2011
Log Cabin Wood Shop - Inside Work
Now that the roof is done* and water tight, we had a chance to start working indoors this week. None too soon, because we have had snow a couple of days this week. So, we installed the electrical wiring, layed down a visqueen vapor barrier in the crawl space, insulated the floor, and installed and stained the 2x6 flooring. Then we insulated the ceiling and gable end walls. And installed the wood stove triple wall pipe and mounts.
You'd think that now we'd have a warm cozy cabin, wouldn't you? Well it is certainly easier to get warmer (from last night's low of 9 degrees), but we still have tarp for a front door and clear plastic covering the windows, so keeping the heat in is a challenge even with insulation.
So tomorrow is door day. I plan to make a nifty

dutch door (just like Dick Proenneke's Alaska cabin less wooden hinges). For those of you not familiar with Dick's story, I highly recommend you read "One Man's Wilderness, An Alaskan Odyssey", quite inspiring.
* Roof is covered with tar paper
awaiting arrival of the metal roofing material
Tuesday, November 8, 2011
Log Cabin Wood Shop - Log Porch
Next task is to lay the 1x8 T&G boards (pre-stained by Debbie) on top of the rafters, put up the facias, and cover it with tar paper. Then I start on electrical until the metal roof arrives.
Thursday, November 3, 2011
Log Cabin Wood Shop - Weatherproof Roof roof roof
The perimeter overhangs are covered with 1x6 pre-stained boards, so we won't have to stain those nasty soffits from a ladder getting a kink in our necks.


Deb then covered the windows and doors with plastic to further keep rain and snow from blowing in. We have the windows and will install them once we get the porch done. That door looks pretty slick, eh?
Today I started on the porch logs.
Saturday, October 29, 2011
Log Cabin Wood Shop - Roof Frame Completed
There are two doubled 2x8 cross beams spanning the width of the shop, on which I have 5x5 posts sitting to help support the ridge.
Today was plane and stain day. I needed to plane about 50 1x6's down to close to 1/2" to be used for the exposed soffits. The rest of the roof not seen will be 1/2' OSB. I also had to plane (10) 6 1/2' house logs removing the tongue and groove, to be used for the porch rafters.
We also finished cutting the last porch beam support log posts, 4 total about 10" diameter. Deb spent the last several days removing their bark and using the draw knife to get them down to the wood for a "skip planed" look.
Debbie also did a ton of staining as today may be the last "warm" day of the season (above 50 degrees). This included the porch rafters, all of the soffit material and the facias. So everything will have one coat of stain going into winter.
Next job is to put in the front deck joists and flooring in preparation for the log posts and beam.
Friday, October 21, 2011
Log Cabin Wood Shop - Roof Begins
Today we set the gable ends (triangle pieces on the end of the building) on top of the log walls. To do this I erected a "boom" onto the tractor's loader. Deb guided the gable ends into place and I gently set them on top. I pre-built the gables in the garage including OSB (oriented strand board) sheathing and the Tyvek house wrap covering the OSB. There is a notch at the top of each to hold the ridge beam. They were pretty heavy, so I wasn't exactly sure that the boom arrangement would actually work... but it did great!
Up until today, we've been busy bleaching, trimming, caulking and staining the logs. The bleach/water mixture (1:3) did wonders with the sun-darkened logs. I included a "before" picture below to show the difference.
So now, we have one coat of stain on the outside (using Permachink's Lifeline "Dark Natural" stain), and one on the inside using Behr Log stain. Deb did most of the staining. We caulked before staining using a latex/silicone combo caulk which matched the stain really well. Now, aside from missing the roof, the cabin is winter ready. we want to get one more coat of stain on the outside before it's too cold to stain.
Next job will be to put up the ridge beam and start setting rafters into place.
Wednesday, October 12, 2011
Log Cabin Wood Shop - Log Walls Completed
courses using about 100 logs. I am looking forward to starting the roof.
Next step for the roof is to build the ridge beam and post structure. We also need to get the log porch beams and posts done and up.
You'll see that the logs extend on the gable ends longer than the normal amount. This is to accommodate an 18" roof overhang. The ridge beam will extend the same amount.
Those last few top lops were quite a stretch for the tractor, even with the forks. But it really helped get the logs high enough, so all I had to do was lift the ends into place.
We ordered some log stain (Permachink Lifeline Dark Natural), and we hope
the weather will continue to be nice enough to get the logs cleaned, bleached, caulked, and stained before winter.
Fall is definitely here, with cooler days and nights, but for the most part it has been clear and nice. We plan to get a little more golf in before winter, so tomorrow is a day off. We also are planning a trip up to Colville to Webley Lumber to get the rafters, 2x6 tongue and groove flooring, and other lumber to frame in the roof.
Tuesday, October 4, 2011
Log Cabin Wood Shop - Taking Shape
These house logs were pretty inexpensive (relatively) so I expected to have some that were bowed, warped or twisted ... and I was not "disappointed", although so far most are ok. I did have a problem with a hump along the back wall that I dealt with using a hand planer. At the
Meanwhile, Deb continues to debark logs. We took down a second standing dead tamarack tree, which turned out to be too big in diameter and too curvy. We may get one or two of the posts at the top end, then save the remaining log for the house. She used a spud and a draw knife to do the debarking.


Friday, September 30, 2011
Log Cabin Wood Shop - Walls Begin
As of today, we have 4 of 18 log courses done. It seems slow, but the cool thing about log buildings is that once the walls are up, you're done ... no siding, no insulation, no interior work.
Before I started the first course, I installed some really straight 2x4's in each corner and in a few other spots, and made them perfectly plumb, so as we put up the logs, (hopefully) we keep the walls plumb, straight and level. We'll see.
Before a new course is put down, I lay down some 1/2" thick foam tape and a bead of caulk along the length of the top of the previous log.
We carefully place the new log on top. The logs are then screwed down using 9" "Olylog" screws every 30" along the log, which I drive in and counter sink with a hole hawg drill motor.
Once the logs are screwed down solid, the corners are pegged using 1" round x 5" long dowels embedded in caulk. This creates a spline of sorts in each corner and in butt joints to keep the logs from twisting. It also seals the corners where one log butts up to another, so water, air and bugs won't come inside... as much. In a traditional round log home, you typically have interlocking notched corners, so you don't have these butt joints to seal.

We also cut down a dead standing tamarack tree and dragged the lower 30' to the shop. 26' of that log will be used as the porch roof header/beam supported with (4) log posts. Deb is going to debark it beginning this weekend.
We also cut down a dead standing tamarack tree and dragged the lower 30' to the shop. 26' of that log will be used as the porch roof header/beam supported with (4) log posts. Deb is going to debark it beginning this weekend.
Saturday, September 24, 2011
Log Cabin Wood Shop - Foundation Complete
Today we finished the foundation frame for the shop. It was pretty dusty work, wallowing around in the trenches setting posts and putting in bracing, but it's done. I'm calling this design the "integrated post and beam" foundation because it takes advantage of the 6x6 cross beams (D logs) to help strengthen the overall base.
We (i.e., Debbie) still have some grading work to do around the perimeter, which should get done tomorrow. We also need to cut down a couple of standing dead tamarack (larch) trees to use for the porch posts and header. Tamarack trees tend to be long and straight with less taper than fir or pine. Deb said that she'd debark them, while I start work on the walls.
Tomorrow I need to peg the corners and joints for the first layer already done and built some plumb guides to I keep the walls plumb as they get higher. (more on this later)
This is a draft of what the shop layout will look like. Is 16x24 big enough? Heck no, but it's bigger than my last shop.

Tuesday, September 20, 2011
Log Cabin Wood Shop - Foundation
The foundation for the wood shop is about 1/2 done, after 3 days work. (We took the last two days off and visited Spokane and played some golf in Chewelah).
We have 13 of the 29 posts set, creating the basic 16' x 24' frame of the base.These posts are 6x6 treated with a "retention level" of .60 pcf. This refers to the amount of preservative that remains in the wood after the treatment process is complete. It is measured on a weight basis and is typically expressed as pounds of preservative per cubic foot (pcf) of wood. The frame is now squared and level, so the remaining 16 posts are relatively easy to install. Even though this is dusty ditch work, it is fun and rewarding to see things come together.
The base foundation structure is built like a wooden roller coaster - with everything tied together and braced at all angles for shear strength. The first layer of logs are part of the frame structure - anchored to the posts and braced. Since the posts are set 36" deep, once back filled, the earth will provide even more shear strength.
I expect that we'll be finished with the frame in a few more days and then we can back fill them. then the real fun begins - setting up the log walls. Here are the 16' D logs stacked are ready for set up.
Thursday, September 15, 2011
The Log Cabin Wood Shop - Genesis

Debbie and I have embarked upon another project which is a Log Cabin Wood Shop. It will be 24' x 16' with a 5' deep porch along the long side (similar to the look of the cabin). The roof will have a 6/12 pitch on the main part and 3/12 on the porch. It will have two windows and one 4' wide front door that I plan to make, and I'll install a small wood stove inside.
I had already purchased 130 6x6x16' 'D" logs from a local supplier at a bargain price and today we dug out the foundation ditches with a rented excavator. I also have the 9" log screws and sealing tape to got between the log courses.
The logs will be stacked in the "butt and pass" method.The foundation will be built using 6x6 treated posts every 4 feet on piers set about 3' deep. The log walls will sit on the top of the 6x6 posts. the foundation walls will be skirted with 2x6 and 2x8 treated wood.

Once done I'll be able to move all of my wood working power and hand tools, as well as benches inside so I can
start turning bowls and doing other projects again. I am looking forward to having a shop again so I can work in a heated space. We should be able to get it "framed in" with at least tar paper on the roof before winter really sets in. After all, we still need to play golf and have fun too!
Sunday, July 17, 2011
How (most) Ultra-Light Travel Trailers are made
The floor assembly is based on an aluminum frame enclosing foam insulation, with 5/8” plywood screwed to the frame and linoleum laminated on top. The chassis is then flipped upside down, and the axles, wheels, and underside wiring, plumbing, and heating ducts are installed on the bottom side of the chassis. In some models extra insulation and heating ducts are added to aide in winter camping. This mess is then covered with a layer of corrugated plastic material which encloses the bottom side, keep out some cold and helping
to reduce wind drag.
The trailer is then flipped back upright for the construction phase. At this point the interior walls, cabinets, framing are installed onto the floor. These elements are screwed down to the
plywood floor. Next, kitchen and bath components are installed into the trailer and plumbed in. Wiring to the cabinets and lighting, and plumbing is completed to the sinks, shower and toilet.
Once the interior items are installed, the walls can be erected onto the floor. The front, rear and side walls are built separately, based on a framing made from 2” square tubular aluminum material.
Rigid foam insulation is cut to fit inside the frame and layers of fiberglass is laminated to the outside of the frame. Luan plywood and a layer of laminate material is laminated to the inside, completing a one-piece wall assembly. The wall is then lifted into place and screwed down to the floor. The other three walls are built and attached in the same manner.
An aluminum framed roof assembly is built similarly to the walls, but in many cases, could have either a flat roof or arched steel trusses to create curved roof. The roof is covered with EPDM rubber which us glued down to make itwaterproof. Roof vents and an air conditioner is added and screwed down and sealed.
Slide outs are assembled separately and mounted to the trailer.
Doors and windows are installed and sealed.
Graphics are placed on the walls.
Doors and windows are installed and sealed.
Graphics are placed on the walls.
Meanwhile, people are com
pleting the interior, mounting and wiring the electrical panel, lighting, heating, microwave, oven, televisions, mirrors, drawers, cushions, and carpets.
Once the trailer is complete, a quality assurance inspector goes over the inside and out, marking anything that isn't correct with pieces of red tape. Cabinets, marks, scratches, etc. Then someone goes back in and corrects the defects.
Once the trailer is complete, a quality assurance inspector goes over the inside and out, marking anything that isn't correct with pieces of red tape. Cabinets, marks, scratches, etc. Then someone goes back in and corrects the defects.
Subscribe to:
Posts (Atom)